In short, a former is a “horizontal multistage forging machine.”
Supplied materials, such as bars and coils, are cut to a certain size before being transferred between plural facing tools. These materials are molded as they pass through several stages of the machine. Pressure is applied and a shape is formed.
Technology Information
About Formers
Parts that are formed by the punch and die in the former are called blanks.
When the die and the punch “transcribe the shape” of the material, the KO system begins to operate, and the KO pin kicks out the blank from inside the die.
When the die and the punch “transcribe the shape” of the material, the KO system begins to operate, and the KO pin kicks out the blank from inside the die.
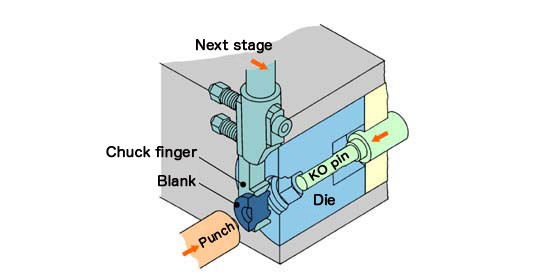
Formers use plasticity deformation (*1) processing to form, but in order to obtain the necessary shape, a shearing process (*2) is also carried out. These forming methods will be introduced below.
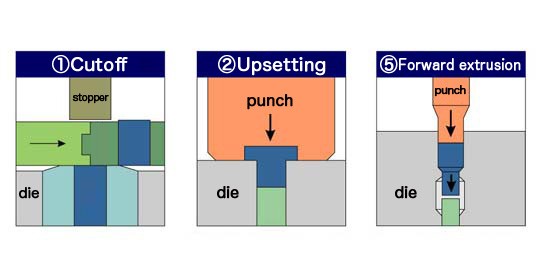
As a forging machine, one of the greatest features of a former is its material cutting function.
For example, in a press machine, material (such as bar material) is cut and heat treated, and a surface (lubrication) process is conducted. Slugs, which are made for a press, must be placed in the press after they are manufactured.
Formers cut coil or bar materials inside the machine to a predetermined size and shape. The cutoff blank is transferred, “as is,” through the transfer process. Through multiple processes, crude material is turned into precision parts.
Formers cut coil or bar materials inside the machine to a predetermined size and shape. The cutoff blank is transferred, “as is,” through the transfer process. Through multiple processes, crude material is turned into precision parts.
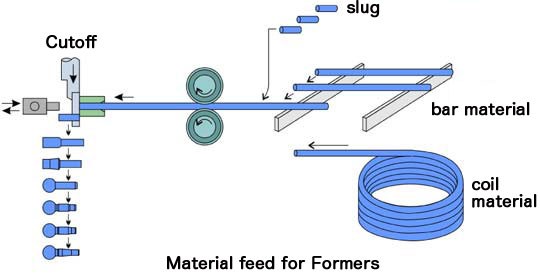
Different temperature ranges are used when forging, depending on the properties and shape of the piece to be worked on. Depending on the temperature, there is cold, warm, and hot forging.
Formers used in cold forging are called, “cold formers.” Warm forging formers are called “warm formers,” and hot forging uses “hot formers.”
Formers used in cold forging are called, “cold formers.” Warm forging formers are called “warm formers,” and hot forging uses “hot formers.”
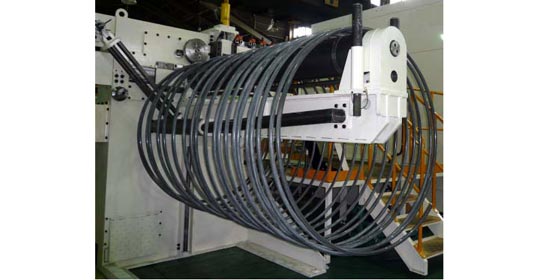
Formers combine various processes such as forward extrusion, backward extrusion, and upsetting to form complex shaped blanks.
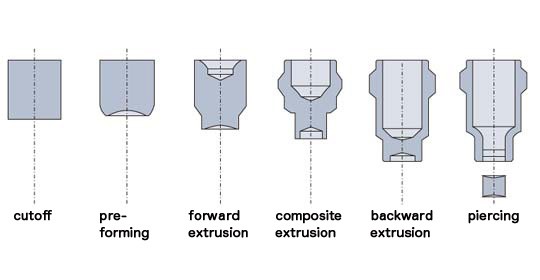