Technology Information
Focus on Safety and Environment
Usually coiled wire material is used on the formers. Coiled material is bundled with steel bands, and whenever cutting this steel band, spring back causes bundled material gets burst all at once, and it is very dangerous to operator. Especially, it is high risk to cause serious injury to operator on the large size machine.
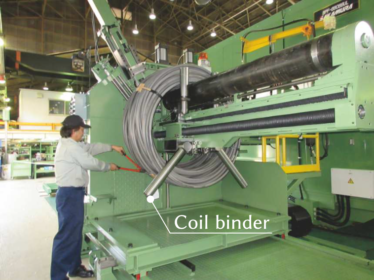
Lubricating oils and cooling oils play such a crucial role in the smooth operation of formers.
Oil deteriorating or clogging pipes due to contamination of foreign matters could lead to seizing because of not securing of the required amount of oil supply.
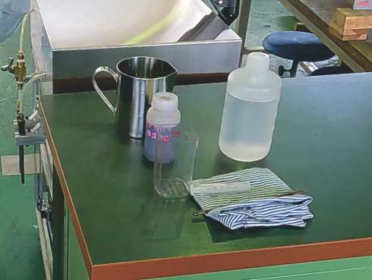
Oil is essential for the operation of formers. Using clean oil reduces wear on parts and prevents seizing breakdowns due to clogged pipes.
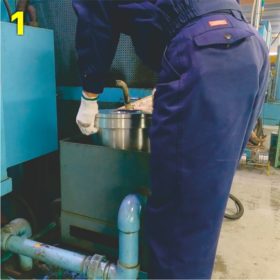
Bonderizing is a pretreatment process of putting a lubricating film on the surface of the material, which has an important function of reducing the friction that occurs between the material and the mold during forging and preventing seizing. On the other hand, this can cause oil contamination and floor stains if this scatters as powder.
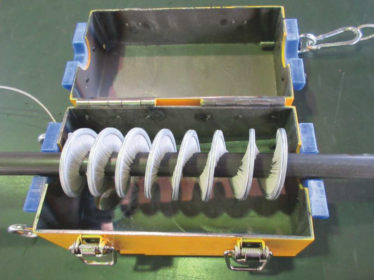
Coiled wire is normally used on our formers. The wire is bound by a band, but when this band is cut, it springs back instantly and is extremely dangerous.
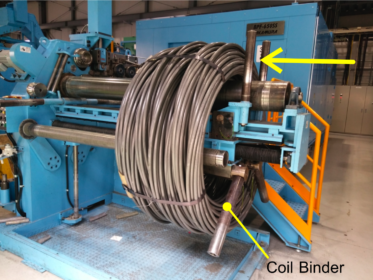
With formers becoming more compact, oil tank capacity tends to be reduced.
In order to maintain the cleanliness of lubrication oil, a seal is installed on the slide, allowing it to be separated from coolant oil.
In order to maintain the cleanliness of lubrication oil, a seal is installed on the slide, allowing it to be separated from coolant oil.
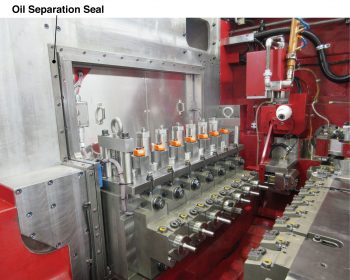
In order to make adjustments to the punch, an operator must enter the forging area to perform the necessary work. This can be unsafe on typically-used, unstable scaffolding.
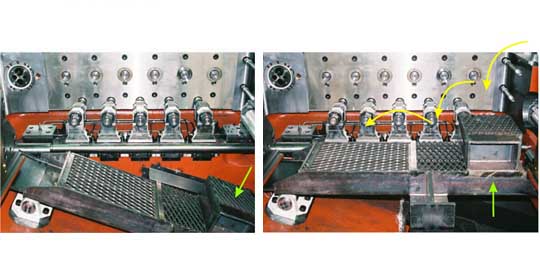
We recently have had requests from customers for compact formers. Saving space in the factory, an increasing number of companies expanding overseas, and labor during relocation are all reasons for this type of former’s recent popularity.
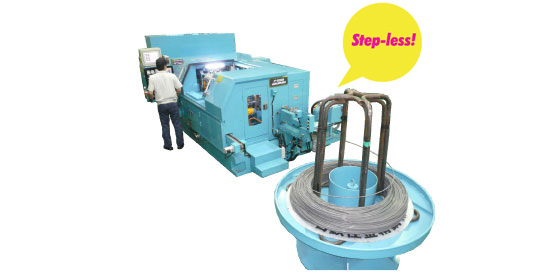