技術情報一覧
高精度成形
フォーマーにより生産される部品は精密化が進み、ネットシェイプ化されることが多くなっています。
サカムラでは、成形後の製品の打痕傷を削減する「SPコンベア」を開発していますが、圧造部品のさらなる高精度化に対応するため、SPコンベア後の打痕対策にも配慮したSPラインを製品化しています。
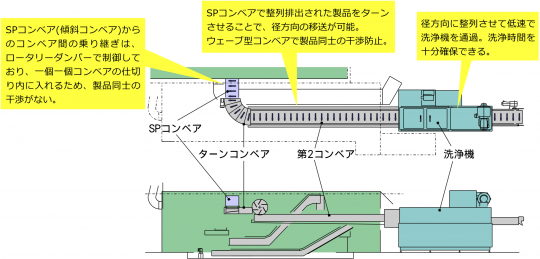
個別式ダイブロックは、各工程のブロックを独立させて隙間を設けています。
そのため、圧造時に発生する熱の影響が隣の工程に及ぶのを抑え、ダイブロック全体の熱膨張を抑制することができます。
これは、ダイブロック内のクーラントオイル配管と併用することで、より効果を上げることができます。
そのため、圧造時に発生する熱の影響が隣の工程に及ぶのを抑え、ダイブロック全体の熱膨張を抑制することができます。
これは、ダイブロック内のクーラントオイル配管と併用することで、より効果を上げることができます。
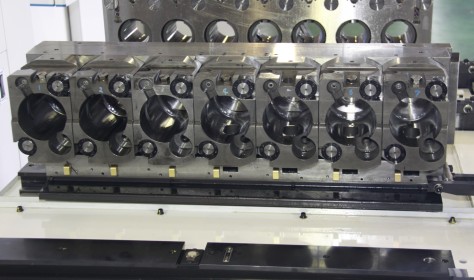
美しい製品成形のためにはバリが悪影響を及ぼさないことが求められます。特にベアリングレース成形においては、バリの打ち込みは忌避されています。
サカムラでは、上記の問題を『ゼロサポートシステム』で解決しました。
サカムラでは、上記の問題を『ゼロサポートシステム』で解決しました。
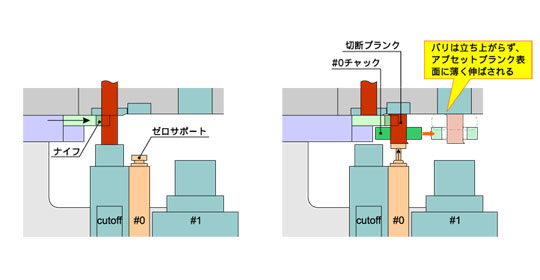
安定した一体のオーバーアーム型ラムです。
スケール・冷却水のラム摺動面への混入防止のため、ラム前面にエアーシールとグランドパッキンを取り付けることで、ラムスライドの長寿命化を図っています。
スケール・冷却水のラム摺動面への混入防止のため、ラム前面にエアーシールとグランドパッキンを取り付けることで、ラムスライドの長寿命化を図っています。
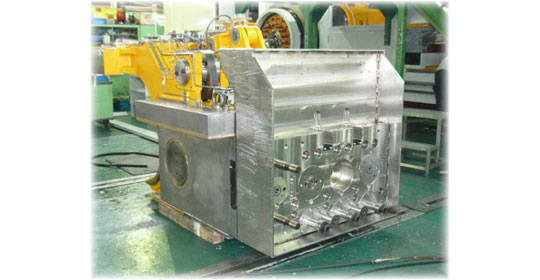
フォーマーの稼働中は、圧造荷重によってフレームに歪みが発生したり、ライナー部が内側に引っ張られたりすることがあります。それに対応するためには、応力集中部に十分な強度を持たせることが重要です。
例えば、圧造圧力21,000kNのフォーマーの場合、それに耐えるフレーム重量は150トン以上にもなります。
そこでサカムラでは、加工、運搬を考慮して、三分割のフレームを開発し、高剛性を実現しています。
例えば、圧造圧力21,000kNのフォーマーの場合、それに耐えるフレーム重量は150トン以上にもなります。
そこでサカムラでは、加工、運搬を考慮して、三分割のフレームを開発し、高剛性を実現しています。
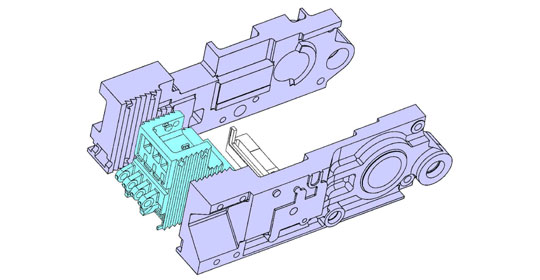
SPコンベアーは、フレームを貫通したコンベアーに製品をソフトランディングさせることで、成形された圧造製品が、金型またはチャックから落下したときにできる打痕傷の発生を防止します。
作業台のすぐ下をコンベアーが製品を搬送しているので、作業台に設けたチェック用の窓を開けて、その場ですぐに製品チェックすることができます。
作業台のすぐ下をコンベアーが製品を搬送しているので、作業台に設けたチェック用の窓を開けて、その場ですぐに製品チェックすることができます。
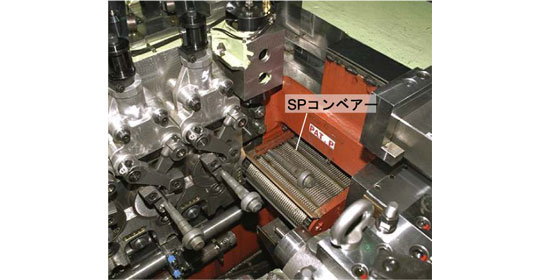
ステンレス材を加工するには温間鍛造が適しています。
温間鍛造は素材を300~750℃に加熱してから加工する鍛造ですが、温間フォーマーでは、通常200~600℃付近で行われています。
サカムラフォーマーは、インダクションヒーターを装備して、温間仕様にすることが可能です。
温間鍛造は素材を300~750℃に加熱してから加工する鍛造ですが、温間フォーマーでは、通常200~600℃付近で行われています。
サカムラフォーマーは、インダクションヒーターを装備して、温間仕様にすることが可能です。
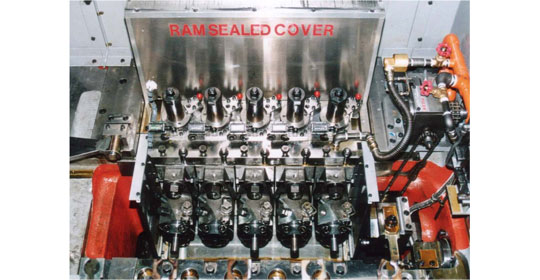
XYトランファーは、X方向に「押し出し」「据え込み」と成形されてきたブランクをダイ内で縦方向に90°ターンさせます。
Y方向に起こしたブランクをPFASのサポートでチャッキングして次工程に搬送し、ブランク側面から加工を行うことができます。
Y方向に起こしたブランクをPFASのサポートでチャッキングして次工程に搬送し、ブランク側面から加工を行うことができます。
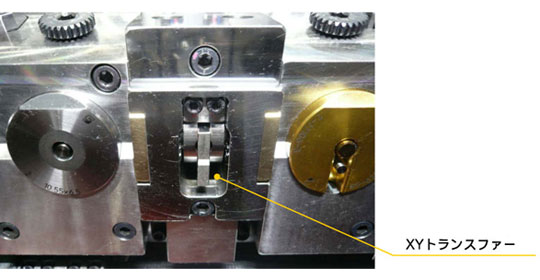
リフィードシステムは、複雑で高精度なパーツの成形システムです。
フォーマーで「切断」→「予備成形」→「ピアシング」などを行ってスラグを成形し、焼鈍により加工硬化を除去し、偏肉精度を高めるため、穴・チャンファーの切削加工を施してからポンデ処理を行い、再度フォーマーに供給して成形します。
フォーマーで「切断」→「予備成形」→「ピアシング」などを行ってスラグを成形し、焼鈍により加工硬化を除去し、偏肉精度を高めるため、穴・チャンファーの切削加工を施してからポンデ処理を行い、再度フォーマーに供給して成形します。
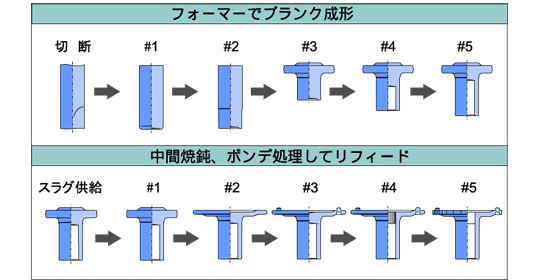
インパクト切断では、インパクト隙間を設けて切断の初速スピードをアップすることで、通常の切断システムより切断速度が2倍以上速くなっています。
この切断スピードの高速化によって、切断面精度の向上を図ることができるのです。
この切断スピードの高速化によって、切断面精度の向上を図ることができるのです。
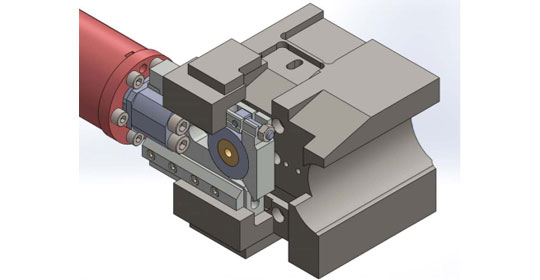